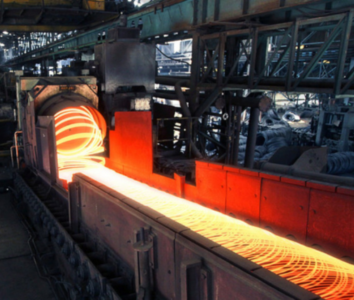
TMT bars (Thermo-Mechanically Treated bars) are the backbone of modern construction. Their high strength, ductility, and resistance to earthquakes make them a popular choice for reinforced steel structures. But have you ever wondered how these essential construction materials are made? The TMT bar manufacturing process involves several stages, starting from raw steel and culminating in reinforced bars that provide structural integrity.
In this blog, we’ll break down the entire process to help you understand how TMT bars are made and why they’re vital in construction projects worldwide.
What Are TMT Bars and Why Are They Important?
TMT bars are a type of reinforced steel used extensively in construction, especially in projects requiring high durability and tensile strength. These bars undergo a specialized process called thermo-mechanical treatment, which imparts strength and flexibility, making them suitable for withstanding high stress and seismic forces.
Their key properties include:
- High tensile strength.
- Corrosion resistance.
- Superior ductility and weldability.
- Better elongation for flexibility during construction.
A Step-by-Step Guide to the TMT Bar Manufacturing Process
The production of TMT bars involves a combination of advanced TMT bar technology and precise engineering. Here’s a breakdown of the steps:
1. Raw Material Selection and Preparation
The first step in the TMT bar manufacturing process is the selection of raw materials. The primary material used is iron ore, along with limestone, dolomite, and coke. These materials are sourced, tested for quality, and then fed into a blast furnace.
- The Process:
- Iron ore is reduced in the blast furnace to produce molten iron.
- Impurities like sulfur and phosphorus are removed through chemical processes.
- The molten iron is converted into steel billets, which serve as the raw material for rolling.
This stage ensures the production of high-quality steel, which is crucial for the next steps.
2. The Steel Rolling Process
The steel billets produced earlier are reheated and shaped into the desired size through the hot rolling mill process. This is where the initial transformation begins, turning raw steel into elongated forms suitable for further treatment.
- The Process:
- The billets are heated to temperatures of 1100–1200°C in a reheating furnace.
- They pass through a series of rollers in the hot rolling mill, which reduces their cross-section and elongates them into steel rods.
- These rods are then cut to standard lengths.
This rolling process determines the size and shape of the TMT bars.
3. Thermo-Mechanical Treatment: The Core Process
This is the most critical stage in the production of TMT bars and gives them their unique properties. Thermo-mechanical treatment involves three stages: quenching, self-tempering, and atmospheric cooling.
Quenching
- Immediately after hot rolling, the steel rods are passed through a quenching system where they are rapidly cooled using water jets.
- This rapid cooling hardens the outer surface of the rods, forming a tough martensitic layer.
Self-Tempering
- The core of the rod, which remains hot during quenching, allows heat to flow outward.
- This process tempers the martensitic outer layer, balancing strength with ductility.
Atmospheric Cooling
- Finally, the rods are left to cool at room temperature under controlled conditions.
- This slow cooling allows the core to retain its ferrite-pearlite microstructure, which ensures flexibility and elongation.
This entire process ensures that the TMT bars achieve the perfect balance between strength and flexibility, making them ideal for reinforced steel production.
4. Cutting and Bundling
Once the thermo-mechanical treatment is complete, the bars are cut into standard sizes, usually 12 meters in length. They are then inspected for quality and bundled together for transportation.
- Inspection Process:
- Each bar undergoes rigorous testing for tensile strength, elongation, and bending properties.
- Bars that meet the specified standards are approved for dispatch.
5. Quality Testing and Certification
Before the TMT bars are sent to the market, they go through extensive quality checks. Testing ensures the bars meet international standards such as ISI (Indian Standards Institute) or ASTM (American Society for Testing and Materials).
- Tests Conducted:
- Tensile strength and yield strength tests.
- Bend and re-bend tests.
- Corrosion resistance tests.
Only bars that pass these tests are certified for use in construction projects, ensuring their reliability and durability.
Advantages of the TMT Bar Manufacturing Process
The advanced technology used in the TMT bar manufacturing process offers several benefits:
- High Strength: The quenching process hardens the surface, making the bars capable of withstanding heavy loads.
- Flexibility: The tempered core ensures ductility, allowing the bars to bend without breaking.
- Corrosion Resistance: The thermo-mechanical treatment prevents rusting, ensuring longevity.
- Earthquake Resistance: The unique properties of TMT bars help them withstand seismic forces, making them ideal for earthquake-prone areas.
- Energy Efficiency: Modern manufacturing techniques reduce energy consumption and carbon footprint, making the process eco-friendly.
Applications of TMT Bars
TMT bars are versatile and widely used in various construction projects, such as:
- Residential and commercial buildings.
- Bridges and flyovers.
- Dams and power plants.
- Industrial structures.
- Underground structures like tunnels.
Their ability to combine strength with flexibility makes them indispensable in modern infrastructure projects.
Why Understanding the TMT Bar Manufacturing Process Matters
For construction professionals, architects, and engineers, understanding how TMT bars are made is crucial for selecting the right materials for their projects. The advanced TMT bar technology ensures durability, safety, and cost-effectiveness, which are all vital for long-term structural integrity.
Whether you’re working on a high-rise building or a simple residential home, knowing the science behind the bars can help you make informed decisions, ensuring your projects stand the test of time.
Final Thoughts
The TMT bar manufacturing process is a sophisticated and meticulously engineered system that transforms raw steel into high-strength reinforced bars. From the initial steel rolling process to the critical thermo-mechanical treatment, every step plays a vital role in producing bars that meet stringent quality standards.
If you’re looking for reliable, high-quality TMT bars for your construction needs, contact Ganraj Ispat today. Our state-of-the-art facilities and commitment to excellence ensure that we deliver the best in the market.
📍Visit us at:
Plot No: A-3, Nagar-Pune Road, Supa Parner Industrial Area, Supa, Parner, Ahmednagar – 414003
📞Call us at: +91 9766173352
📧Email:sales@ganrajispat.com
🌐Website:www.pushpasteel.com
Choose Ganraj Ispat for TMT bars that guarantee strength, durability, and performance!
Recent Comments